Moonlight’s Commitment to Excellence: Quality Control and Manufacturing Process
At Moonlight, we place the utmost importance on quality controlling and monitoring both product and process quality—quality is at the core of everything we do. Our dedication to accuracy, reliability, and perfection drives us to establish rigorous quality control measures throughout every stage of our production process. We believe that superior quality and outstanding after-sales service are essential to building trust with our customers and fostering long-term relationships.
Our LED light housings have been selected by numerous companies and applied in various countries with a stellar reputation. We have built strong, lasting partnerships with customers from the United States, the European Union, Japan, and other regions. This global trust is a testament to our commitment to excellence and our ability to meet and exceed industry standards.
Comprehensive Quality Control in the Manufacturing Process
To ensure our LED light housings meet the highest standards, we follow a structured and meticulous manufacturing process. Every step involves quality checks, testing, and refinements to ensure the final product meets our customers’ expectations. Below is a detailed overview of our manufacturing and quality control workflow:
1. Housing Design & Simulation
The journey of a Moonlight LED light housing begins with design and simulation. Our engineers leverage cutting-edge design software to create innovative and efficient housing structures. During this phase:
- We ensure the design meets thermal management and structural integrity requirements.
- Simulations are conducted to test the product’s strength, heat dissipation, and durability.
- Any design flaws identified at this stage are corrected before moving to the prototyping phase.
2. Making Prototype & Testing
Once the design is finalized, we move on to the prototyping stage, where a physical sample is produced for testing. This phase is critical in evaluating the real-world performance of the housing.
- The prototype undergoes mechanical and thermal tests.
- Stress tests are conducted to simulate environmental conditions such as extreme temperatures, humidity, and mechanical stress.
- If any issues arise, the design is revised, and a new prototype is made for additional testing.
3. Mold Making & Trial Molding
After the prototype passes all tests, we proceed with mold development.
- High-precision molds are created to ensure consistency in mass production.
- A trial mold is produced to verify accuracy, dimensional stability, and consistency.
- If defects are found, we revise and modify the mold before proceeding to full-scale manufacturing.
4. Die-Casting & Surface Treatment
With a perfected mold, production moves to die-casting, where molten metal is injected into the mold to form the LED housing.
- The die-cast parts undergo a rigorous inspection to detect defects such as porosity, cracks, or dimensional inaccuracies.
- Surface treatments such as anodization or powder coating are applied to enhance durability, corrosion resistance, and aesthetics.
- After coating, another inspection is performed to ensure uniform coverage and adherence to quality standards.
5. Assembling & Final Quality Inspections
After surface treatment, the LED light housings are assembled with necessary components.
- Each assembled unit is inspected to verify alignment, mechanical integrity, and proper fit.
- Electrical components, if included, are tested for compatibility and performance.
6. Packing & Shipment
Once the products pass all inspections, they are carefully packed for shipping.
- Packaging is designed to protect products from damage during transit.
- Before shipment, a final inspection is conducted to ensure only flawless products reach our customers.
Rework and Continuous Improvement
Throughout the process, if defects or inconsistencies are found at any stage, rework is initiated immediately. We believe in continuous improvement, and any recurring issues trigger a review of our design, manufacturing, and quality control processes to prevent future defects.
Global Recognition and Customer Trust
Our dedication to quality has earned us a strong reputation worldwide. With customers in the United States, Europe, Japan, and other markets, Moonlight continues to be a trusted provider of LED light housings. By upholding our strict quality standards and offering superior after-sales service, we ensure that our customers receive products that meet their expectations and industry requirements.
At Moonlight, quality is more than just a goal—it is our guiding principle. From design and simulation to final inspection and shipment, every step of our process is carefully controlled to deliver the best LED light housings on the market. Our commitment to accuracy, reliability, and excellence sets us apart, and we remain dedicated to pushing the boundaries of innovation and quality in the LED lighting industry.
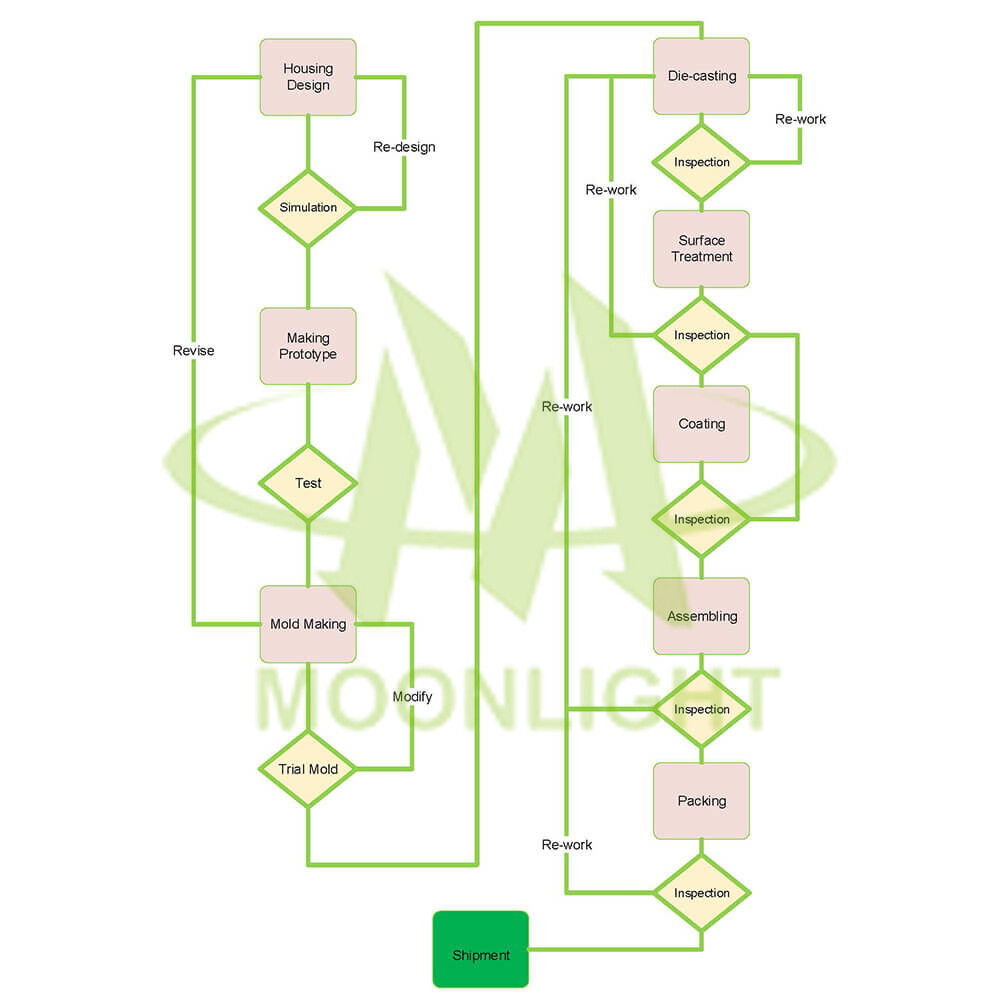