Simple Introduction to Die Casting
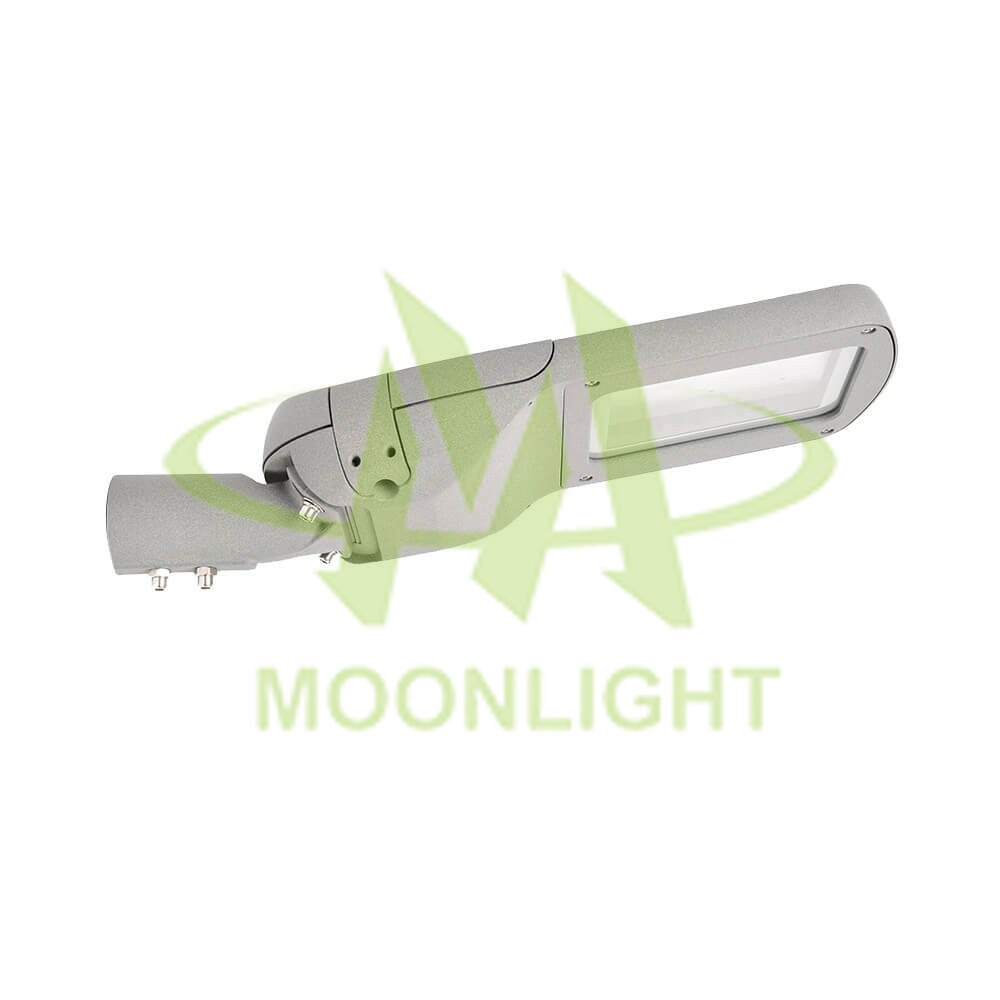
Die-casting is a manufacturing process for producing high volumes of relatively complex metal parts. Die-cast parts are made in steel molds, which is similar to injection molding, but use low melting point metals such as aluminum and zinc. Die-casting is widely used for its versatility, reliability and accuracy. Moonlight technology has been working on die cast for many years and use this process technology to produce thousands of parts.
To create the die-cast part, molten metal is forced into a mold via high hydraulic or pneumatic pressure. These steel molds, or dies, produce extremely complex, high tolerance parts in a repeatable process.
As a die-casting manufacturer and supplier, Moonlight technology is also working on some modern die-casting methods such as squeeze casting and semi-solid metal casting result in high quality parts for nearly every industry. Moonlight technology specialize in casting aluminum and zinc.
Benefits of Die Casting
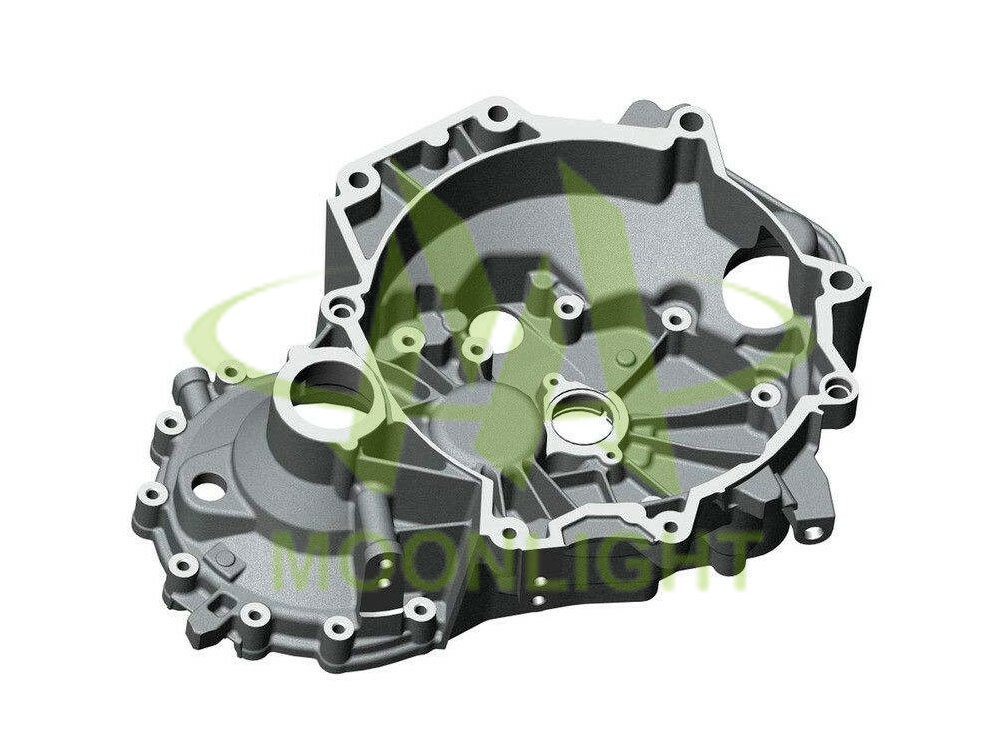
Complex Geometry
Die casting produces close tolerance parts that are durable and dimensionally stable.
Strength
Die cast parts are typically stronger than injection molded parts and more resistant to high temperatures. Moonlight technology can make thinner wall with high strength.
Precision
Die-casting offers tolerances ranging from +/-0.10 ~+/-0.30mm in length from 1mm to 1000mm, and if you have high precision requirements, please contact Moonlight technology since we can make it even as tight as +/- 0.05 on some specific dimensions.
Custom Finishes
Aluminum die cast parts can be produced with smooth or textured surfaces and a variety of coatings and plating finishes. Finishes can be chosen to protect from corrosion and improve cosmetic appearance. All these finish process can be provided by Moonlight technology.
Why Choose Moonlight technology for Die Casting Services?
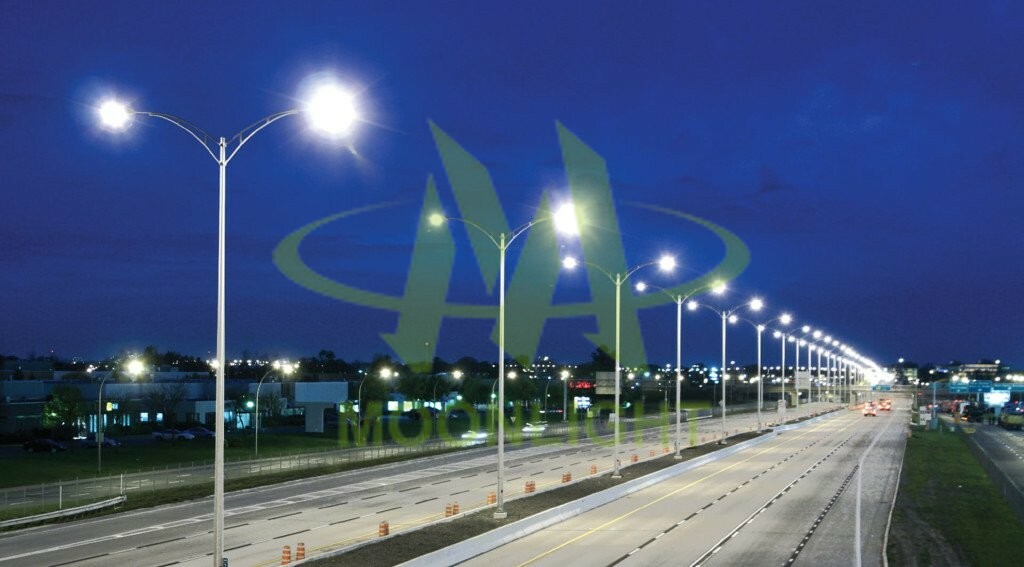
Short Cycle time
As a die-casting parts supplier and manufacturer, Moonlight technology is working on die casting technology for many years and optimized every details to save cycle time. For now, Moonlight technology can shorten the cycle time for 2-3 days, compared with candidates.
Flexible volume production
Moonlight technology is supporting various volume production from hundreds to millions to match the different market needs. And all you orders will be satisfied filled.
Various Options
Moonlight technology has many materials, finishes, tolerances for your choosing. These can accurately meet your special market and small order to test market.
Lower price
Moonlight technology helps customers to save cost from process designs and optimizing. Sometime, use DFM to reminder customers to make some design changes for saving cost.
Types of Die Casting from Moonlight technology
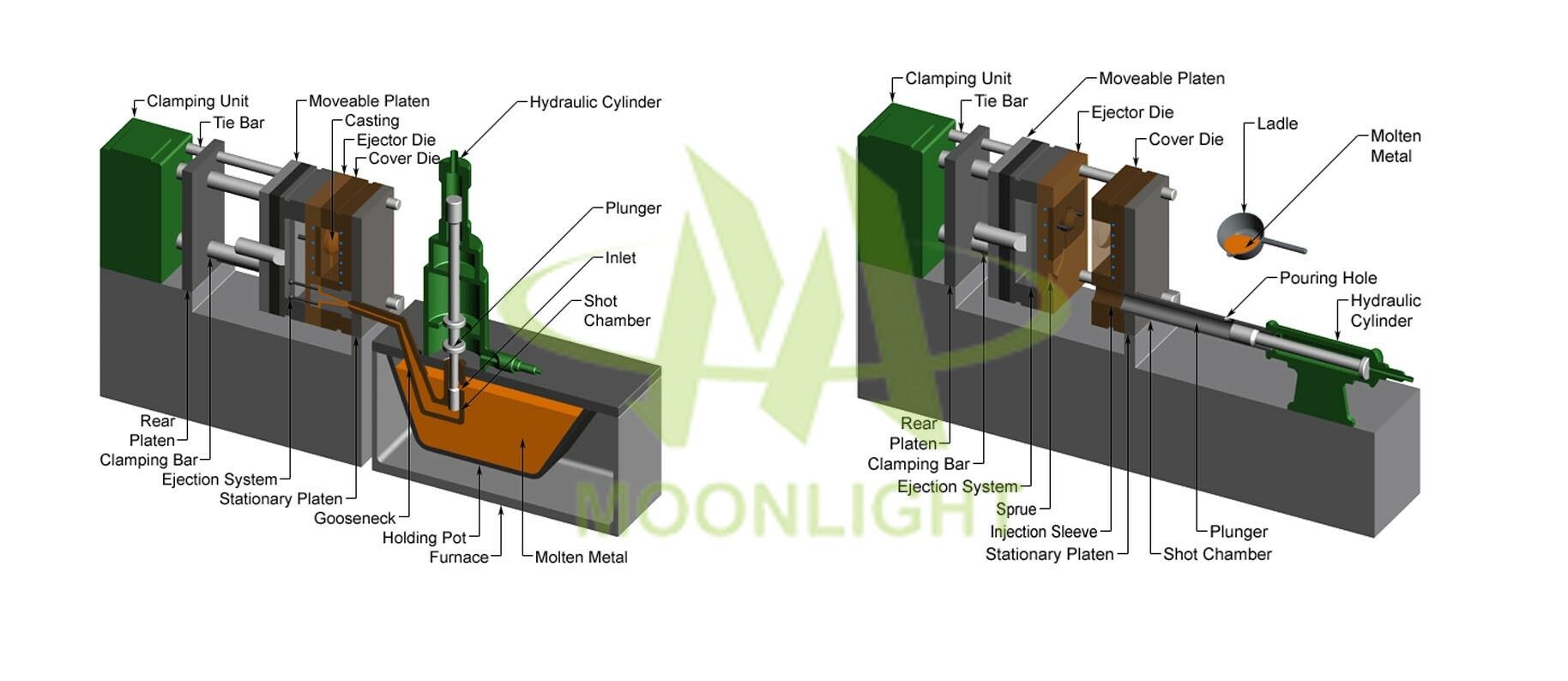
Hot Chamber Die-Casting
Also known as gooseneck casting, Moonlight technology’s hot chamber is the most popular die-casting process. A chamber of the injection mechanism is immersed in molten metal and a “gooseneck” metal feed system brings the metal into the die cavity.
Cold Chamber Die-Casting
Cold chamber die-casting is often used to minimize machine corrosion. The molten metal is ladled into the injection system directly, eliminating the need for the injection mechanism to be immersed in the molten metal.
Die Casting Materials
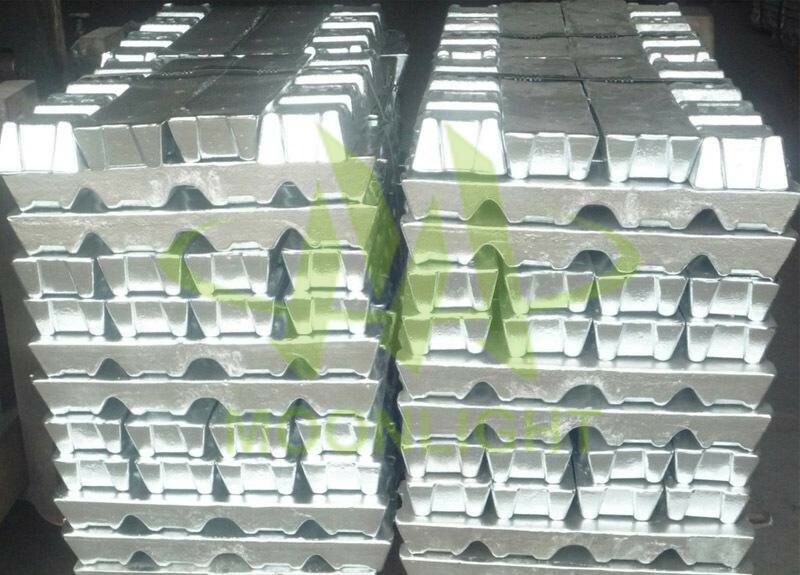
A380 Aluminum Alloy
The most popular alloy for aluminum die casting is A380, also named as ADC12. Moonlight technology uses A380 because it has demonstrably the best combination of physical and mechanical properties for casting, including being lightweight, very strong at high temperatures and corrosion resistant. A380 is also very good at retaining dimensional stability even with complex shapes and thin walls and offers high electrical and thermal conductivity.
A383 Aluminum Alloy
Another option for die casting in Moonlight technology is to use A383 aluminum alloy. This alloy is typically only used when you are forming intricate components it does offer higher strength at high temperatures with less chance of cracking under heat.
ZA-8
ZA-8 is the only hot chamber alloy of the three. It is the zinc-aluminum alloy one uses in die-casting with the lowest possible aluminum content. It features an aluminum content of 8.4 % with 1.0 % copper. Because of the minimal aluminum content, ZA-8 has a lower melting point and higher density than other zinc-aluminum alloys. This makes it ideal for hot-chamber die casting. From experience of Moonlight technology, It’s often used for higher strength requirements that need plating.
ZA-12
ZA-12 has somewhat greater aluminum content than ZA-8, so it offers a sometimes desirable mediation of zinc alloy properties. It has 11% aluminum and 1% copper content. It provides the best combination of castability and strength of the ZA alloys. Because of its higher melting point and lower density. From experience of Moonlight technology, you must use the cold-chamber method if you are using ZA-12 for casting
Die Casting Finishes
As Cast
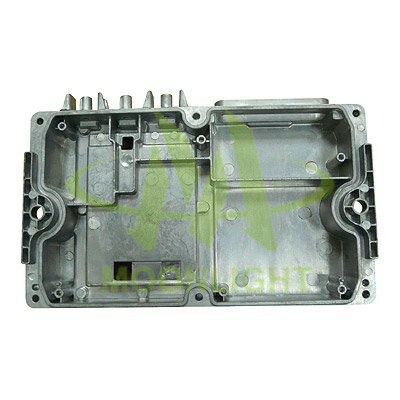
Zinc and zinc-aluminum parts can be left as-cast and retain reasonable corrosion resistance. Aluminum and magnesium parts must be coated to achieve corrosion resistance. Cast parts are typically broken away from the casting sprue, leaving rough marks at the gate locations. From experience of Moonlight technology, most castings will also have visible marks left by the ejector pins.
Anodized (Type II or Type III)
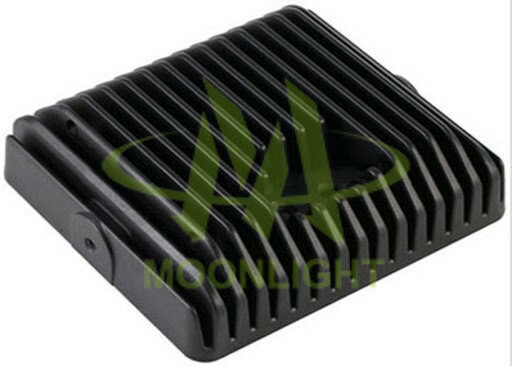
Aluminum is typically anodized. Type II anodizing creates a corrosion-resistant oxide finish. Parts can be anodized in different colors—clear, black, red and gold are most common. Type III is a thicker finish and creates a wear-resistant layer in addition to the corrosion resistance seen with Type II. From experience of Moonlight technology, Anodized coatings are not electrically conductive.
Powder Coating
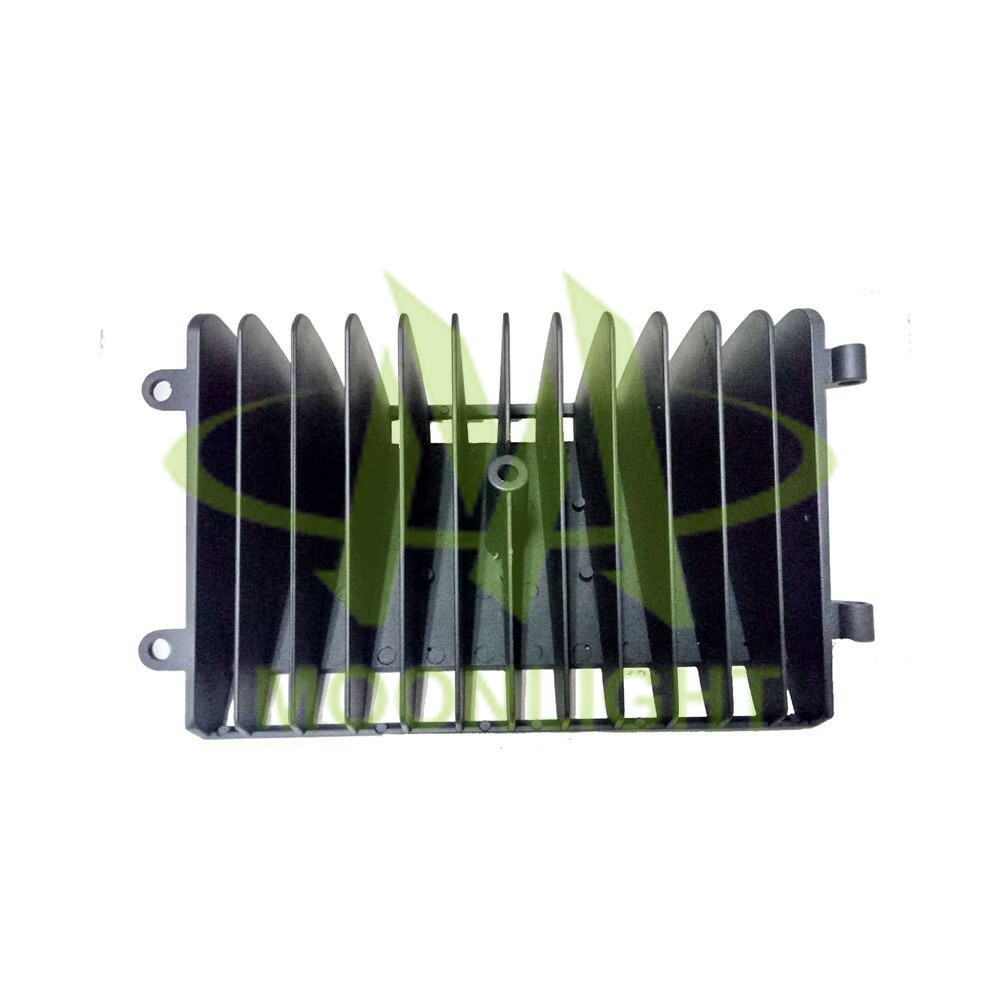
All die cast parts can be powder coated. This is a process where powdered paint is electrostatically sprayed onto a part which is then baked in an oven. This creates a strong, wear- and corrosion-resistant layer that is more durable than standard wet painting methods. A wide variety of colors are available to create the desired aesthetic.
Wet Painting
All die cast parts can be wet painted in a wide variety of paint formulations and colors.
Plating
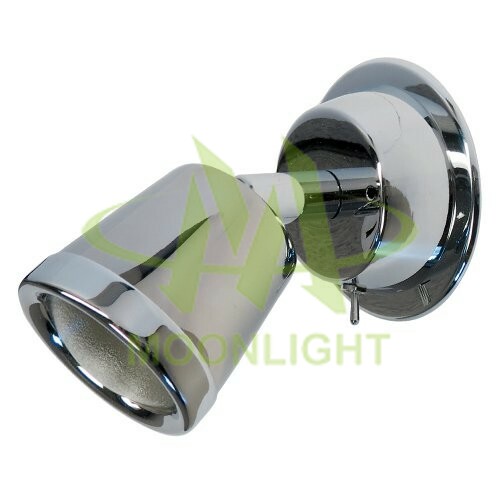
Zinc and magnesium parts can be plated with nickel, brass, tin, chrome, chromate, Teflon, silver and gold.
A chromate conversion coat can be applied to protect aluminum and magnesium from corrosion and improve the adhesion of paints and primers. Chemical film conversion coatings are electrically conductive.
Chemical Film
Applications of Die Casting
Aerospace & Automotive Components
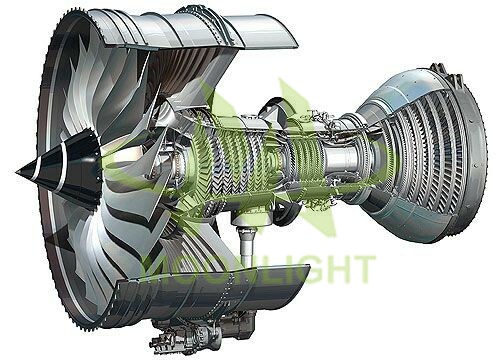
Die casting works well for making components out of high strength aluminum or lightweight magnesium for automotive and aerospace applications. Most parts in these application can be made in Moonlight technology.
Plumbing Fixtures
Moonlight technology‘s top two die casting part is plumbing fixtures. Die cast fixtures offer high-impact strength and are easily plated for plumbing fixtures.
Moonlight technology’s top one die casting part is LED light housing. We use die-casting to make light housings to achieve high strength and lightweight with complex geometry and features.