Die Casting Cosmetic
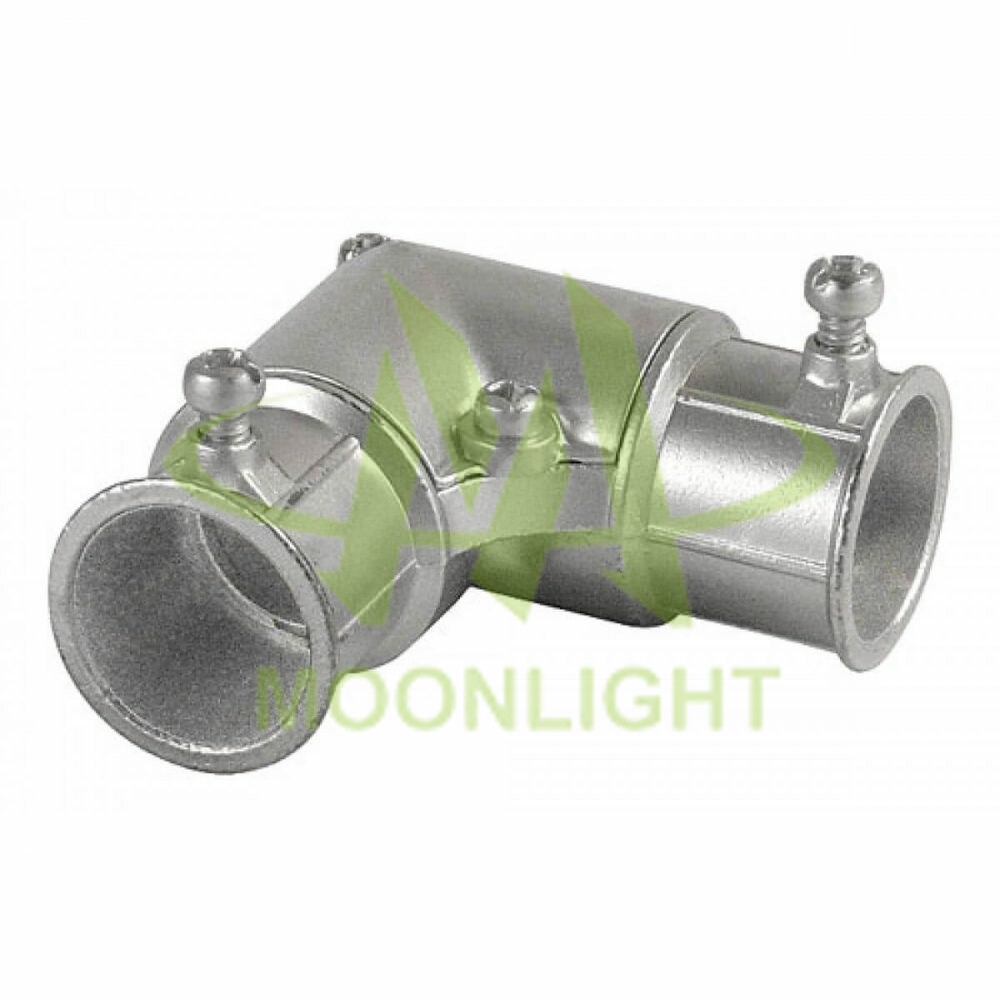
die casting corners
Generally, we always think die casting parts have bad cosmetic and also it is difficult to apply finish processes directly on its surface. Moonlight technology did much work to improve die casting surface, also named die cast cosmetic. These technologies from Moonlight technology can help customers save much cost and finish all the parts in one station. Firstly, we need to aim high cosmetic from features design.
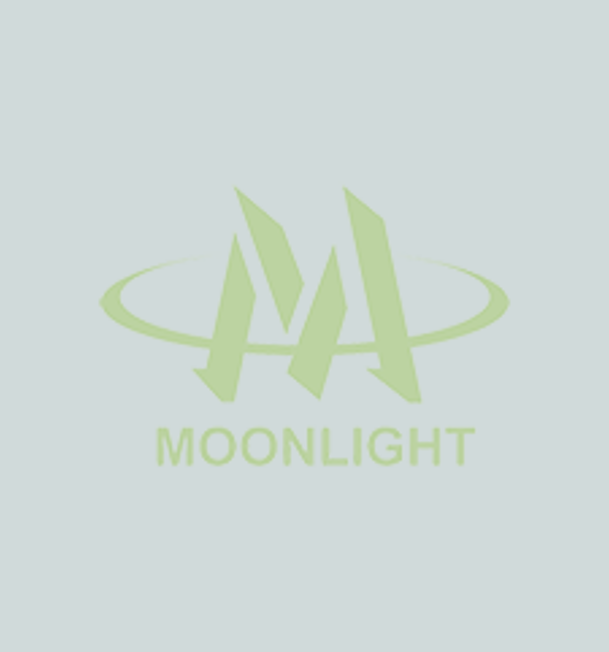
How Die Casting Features Impact Surface Finishing
From Die casting side, where are hidden from view and cosmetically non-critical, can be considered for placement of the parting lines and gating. These features can create significant cost penalties if they are placed on a viewable, cosmetic surface of the parts. Likewise, a potential sink mark on a non-cosmetic surface can be largely ignored, or steps can be taken to overcome its possible appearance by wall redesign—for example, internal support features which will be invisible to the user. Design modifications to aid surface finishing quality are not always feasible, but when possible, they can greatly improve results. In Moonlight technology, these hints will be taken into consideration before manufacture.
Where can improve Die Casting Surface Finishing from Design
1. Die Cast Part Edges
Part designs that hide trimmed edges within the final product assembly eliminate the need for post-casting edge polishing. Early consultation on cosmetic features assures proper placement of necessary parting lines to conceal trimmed visible edges.
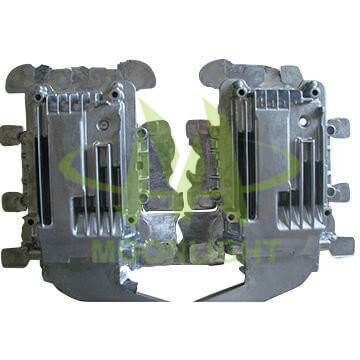
2. Die Cast Holes for Machining
Countersinks (chamfers) or counter bores placed on holes assure the integrity of the surface edge of tapped holes. Leading threads will be protected from de-burring or polishing.
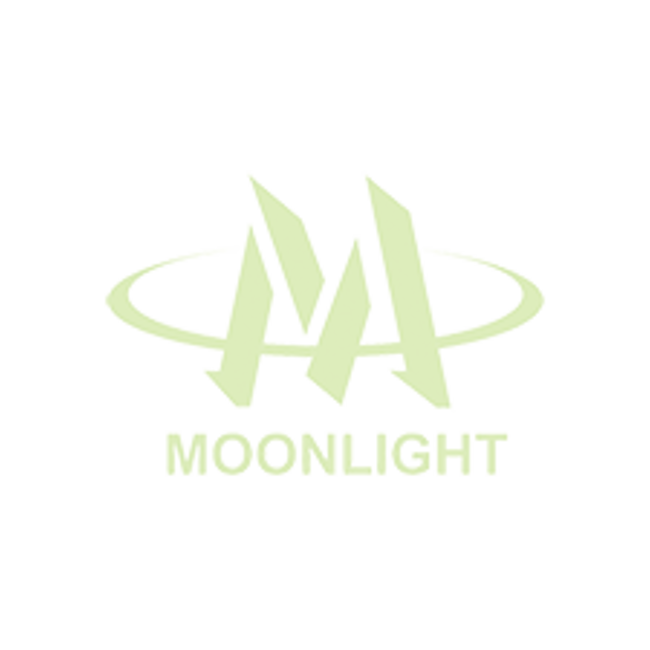
3. Die Cast Mounting Features
Wherever possible, create raised “shoulders” on bosses that will receive painting masks; scuffing thus can be avoided on surrounding painted surface areas during fastener torqueing and mounting of mated parts.
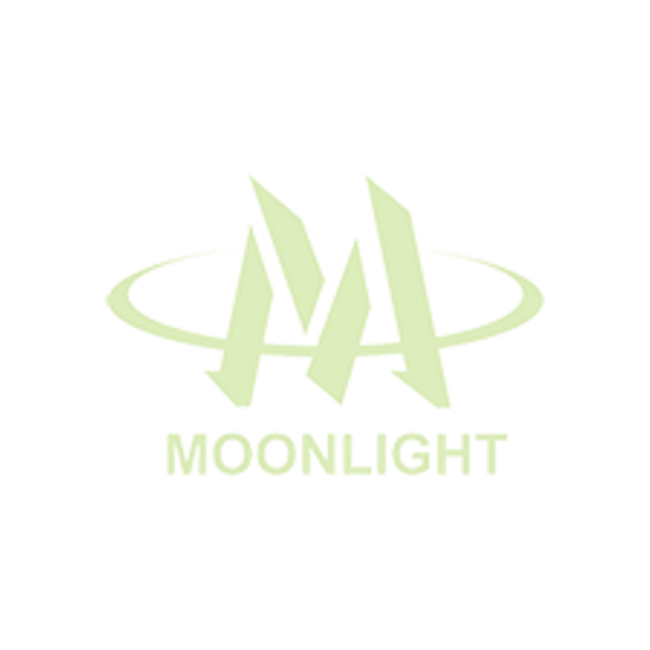
4. Die Cast Bosses
Include correctly designed gussets to improve die fill and avoid resulting sink marks on Class “A” surfaces. Short and stocky bosses are preferable to tall, thin designs to optimize metal flow and insure integrity of the feature.
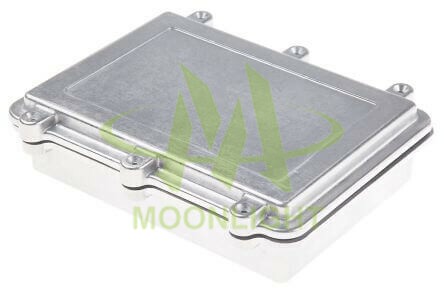
5. Die Cast Corners
Use the maximum allowable radius for all internal and external corners to de-burring tools can reach all part surfaces and also important to assure the complete filling of the die cavity and maintaining the integrity of the corners of the part.
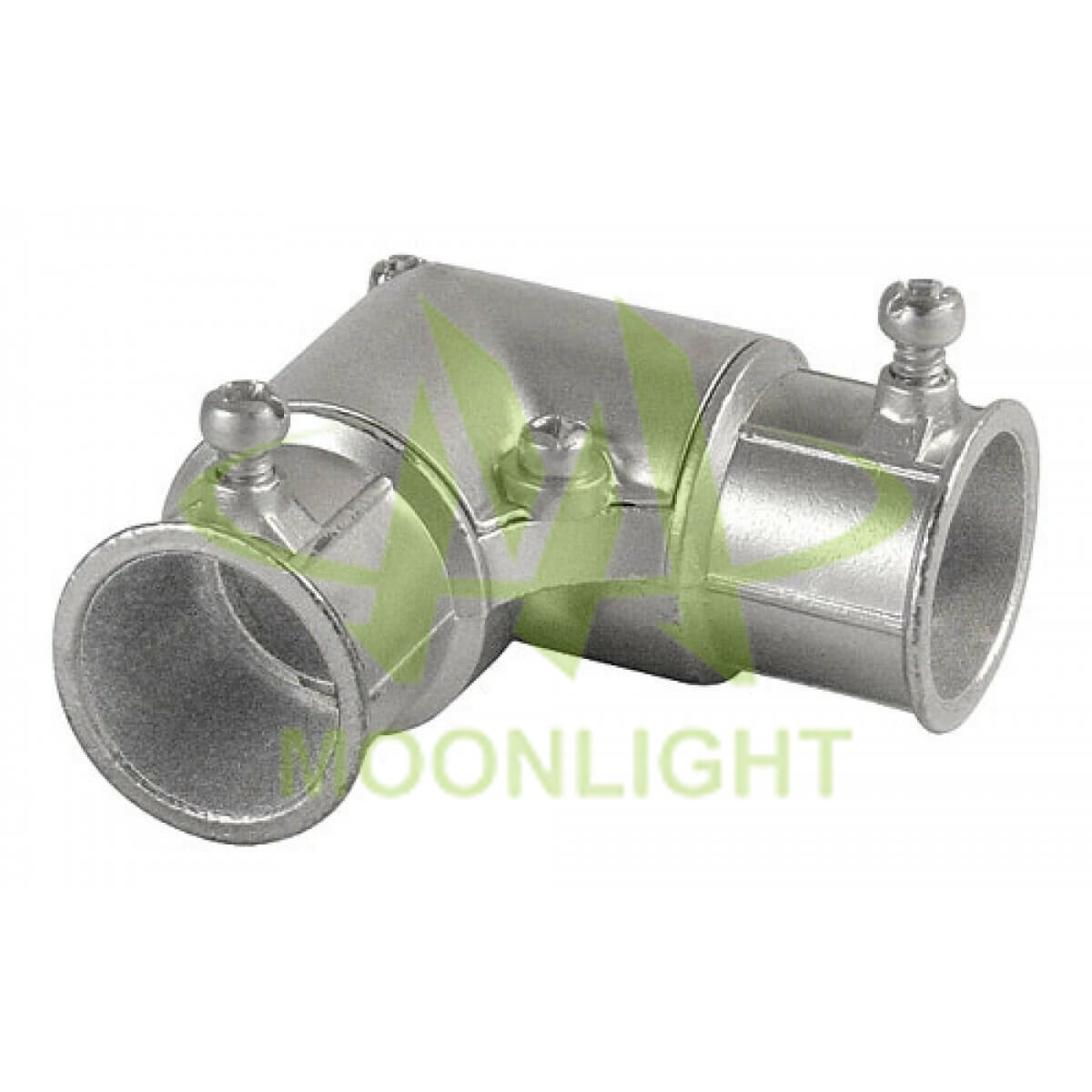
6. Die Cast Surfaces
Subtle textured surfaces can be produced, as-cast, on selected areas of a component by special preparation of the die. These cast-in textures are created by photoengraving techniques during die construction and are sometimes recommended for use on the underside of complex parts to aid in the smooth filling of the die.
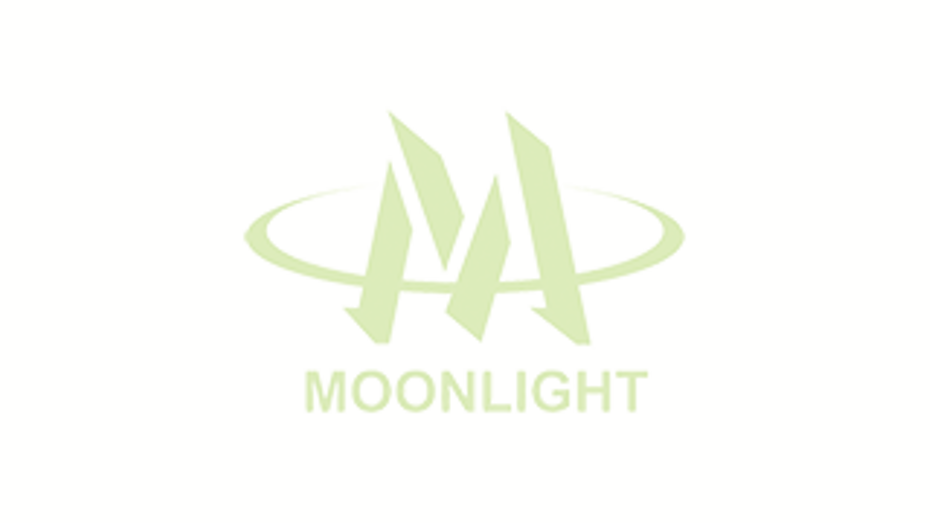